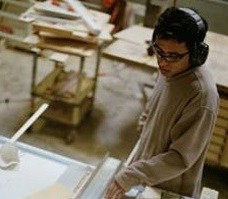
Combating Industrial Deafness Claims
Construction sites and the production floors of manufacturing firms are teeming with the roar of engines and the whine of machines. Without the proper protection, this environment is not only inhospitable, but potentially damaging to workers’ hearing. Prolonged exposure to these types of noise-heavy environments can increase a worker’s risk of developing noise-induced hearing loss, also known as industrial deafness.
From 2013 to 2014, an estimated 80,000 industrial deafness claims were filed—causing some insurers to label the injury as the ‘new whiplash’. While permanent and disabling loss of hearing is a serious injury, there are some claim management firms taking advantage of the diagnosis. For that reason, nearly 90 per cent of industrial deafness claims are rejected, according to the Financial Times. However, as an owner or manager of an engineering, construction or manufacturing firm, you still need to implement an effective industrial deafness risk management scheme. This guidance will protect not only your workers, but your investments as well.
A Quick Overview of Industrial Deafness
Gradual hearing loss is often a by-product of growing older, even for individuals who manage to avoid noise-heavy environments. However, industrial deafness occurs when individuals have been exposed for prolonged periods of time to noise-heavy environments. Permanent, disabling hearing loss and tinnitus, a ringing or buzzing in the ears, are the two most common repercussions of exposure to damaging noise levels of 85 decibels and above. Most tools and equipment used by an engineering, construction or manufacturing worker regularly produce that many decibels or more.
As hearing loss is a common process, for some it can be difficult to discern whether it has progressed naturally or been hastened by the environment. Yet for individuals that have worked in noise-heavy environments, there are four common symptoms that are indicative of industrial deafness:
- Being unable to hear everyday signal noises such as a ringing telephone, the doorbell, etc.
- Having difficulty following conversations, and missing words or whole sentences
- Needing to turn up the volume on the television or radio to clearly hear what is being said
- Hearing a persistent ringing, buzzing or hissing noise in one or both ears, also known as tinnitus
It is estimated that 250,000 workers suffer from some degree of industrial deafness and another one million are at risk. However, the majority of individuals who choose to make an industrial deafness claim generally fail to receive compensation. The most commonly cited reason is not a lack of evidence, but the failure to properly connect the loss directly to their places of work.
Industrial Health and Safety Noise Laws
As an owner or manager of an engineering, construction or manufacturing firm, there are two main regulations related to industrial deafness that protect your workers as well as your investments:
The Noise at Work Act 1963 requires that you conduct routine risk assessments to identify the amount and severity of noise that workers are exposed to regularly. If the assessment determines that there is any potential risk to workers, preventive measures must be taken to ensure their well-being.
The Control of Noise at Work Regulations 2005 (the ‘Noise Regulations’) requires the following:
- Workers need to be provided with well-maintained hearing protection equipment.
- Workers need to receive regular training on how to protect against dangerous noise levels.
- Employers need to provide regular wellness assessments to monitor workers’ hearing.
- Employers need to monitor noise exposure levels and keep them within legal limits—below 87 decibels for daily or weekly personal noise exposure and 140 decibels for peak sound pressure.
Failure to comply with either of these regulations leaves your organisation vulnerable to potentially costly litigation.
Risks Associated with Industrial Deafness
High production of noise is inevitable in an engineering, construction or manufacturing firm—yet the associated risks are not. If, as the owner or manager, you fail to properly assess the potential risks or provide adequate hearing protection for your workers, you risk the following:
For your workers:
- Permanent and disabling hearing loss
- Development of tinnitus
For your organisation:
- Litigation costs and fines
- Damaged public image
While this does not reflect a comprehensive list, it does highlight the most detrimental risks for those involved.
Guarding Against Industrial Deafness Risks
A significant portion of the industrial deafness claims made in recent years are not being filed by current employees, but by individuals that were employed 20, 30 or even 40 years ago. While it is difficult to retroactively protect your organisation and employees, there are several strategies you can adopt to mitigate retroactive industrial deafness claims.
- Maintain well-organised records of any employee wellness programmes that you have instituted over the years. Include any collected results.
- Maintain records of noise-exposure levels throughout your operation. Include the decibel amount that tools and machinery produce.
- Produce a regular report detailing what potential risks have been identified and what measures have been taken to mitigate their damage. Include what safety equipment has been provided to your employees.
- Provide regular wellness assessments to monitor the health of workers’ hearing. Adjust your safety practices if workers’ quality of hearing starts to decline.
High Quality Without High Decibels
Despite some claim management firms sensationalising the diagnosis, industrial deafness is a prevalent concern for engineering, construction and manufacturing firms. To ensure that both your workers and investments are protected, perform regular noise level inspections and maintain well-organised records. For more risk management guidance, contact the insurance professionals at amb Insurance Services ltd today.